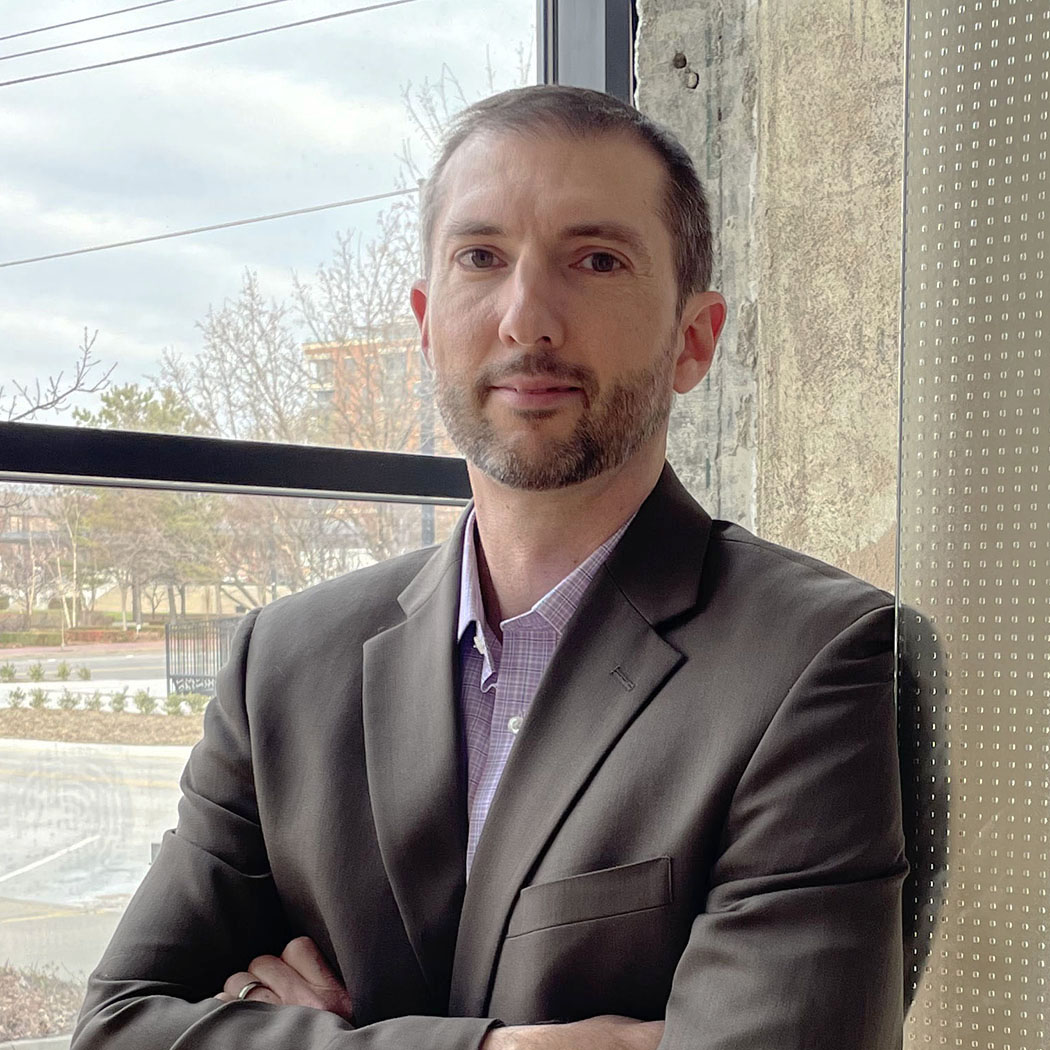
Matt Gebhardt, PE, SE
Principal
Matt received his Bachelor of Science in Civil Engineering, Bachelor of Science in Economics and Master of Science in Civil Engineering degrees from the University…
View Profile
My wife and I do a small amount of gardening and one thing we always plant are some hot chili peppers. Varieties vary depending on what plants we find in the local farm store tent each spring. We almost always have some Hungarian wax peppers, which according to Wikipedia are rated 5,000 to 10,000 units on the Scoville scale (1.5 to 2 times as hot as a jalapeño) and, the last two years, something hotter so we can make and can some hot sauce. This year, we have cayennes as our “hot” pepper, which are 30,000 to 50,000 Scoville units. I at least know enough to stay away from habañeros – 350,000 Scoville! – which is a very good idea, as you’ll see.
So, last Sunday I set out to make hot sauce, cleaning and slicing 30 wax peppers and 20 cayennes – bare handed, making sure to wash up “real good” after I was done. After all, this procedure worked fine last year. Of course, that was a different pepper mix and I only did half as much last time.
Let’s stop and do the math: I’m going to say that’s an average pepper heat of 20,500 this batch. Last year: 12 wax peppers, 10 serranos (10,000 to 25,000) = 12,000 average hotness. So, roughly twice the heat and twice the volume of last year.
I might have averted tragedy had I figured this up front.
My finger-fever broke 18 hours later and I hope to wear contact lenses again some day. Funny thing is it didn’t seem like a problem until a couple of hours after I finished. That’s when the kids told me that the marshmallows I had given them tasted like burning and about the time the tingling in my hands started. Derned if that there capsaicin stuff in the peppers don’t soak into calloused hands like a sponge…and don’t come out no matter how much you scrub.
I do have a point here, beyond highlighting my own stupidity. Most of the time, a few simple questions, maybe some quick calculations, and a little forethought can save yourself and your team a good deal of extra work, aggravation, and, dare I say, pain.
I get a lot of requests to review and provide details for interior tenant improvement projects. The most conspicuous culprits are light gage steel framing, suspended ceiling systems, hanging loads, and new roof mounted mechanical equipment.
– Suspended ceilings:
Some high seismic jurisdictions may not require a structural engineer for suspended ceiling systems, but will say they must take into account lateral loads, or some such ambiguous statement. The best source for information on this is a technical document published by the Ceilings and Interior Systems Construction Association (CISCA) called Seismic Zones 3-4 Guidelines for Seismic Restraint for Direct Hung Suspended Ceiling Assemblies. Included are prescriptive requirements that can be used in lieu of an engineered system and sample details. Many jurisdictions accept systems detailed to these prescriptive requirements.
– Interior light gage steel framing:
Most of the input I provide on light gage framing details isn’t anything calculated. It’s stability and constructability.
Stability: In engineering circles, we ask, “Is there a clear load path?” That’s just engineer speak for, “Is it going to fall over?” A few simple questions can drastically improve the safety of light gage framing:
1. Are walls braced or otherwise supported at the top? Corner braces don’t count, mostly. Walls with nothing at the top cause the top track to act like a girt. If your track will support the load until it gets to an intersecting wall, this can work, but don’t count on getting more than a few feet out of it. Adding a corner brace only shortens the distance the track needs to span.
2. Are bulkheads hanging from something sufficient or supported from below on a header? Watch out for situations where the center of gravity of the assembly is far from what is supporting it.
3. Do headers have jambs to support them? It seems obvious, but it’s easy to add a header in section and forget about what’s going on at its ends in plan.
4. Are there any sections that will behave like a hinge and be unstable? Unless it’s a connector specifically designed to form a rigid connection, assume it will behave like a hinge. Tremendous shearing stress can be put on a four-screw group when the connected element is a lever.
Constructability: Again a few simple questions, such as these, can really smooth out construction.
1. Back-to-back stud connections and stud-to-track connections are the most economical to make. There are connectors for just about any condition, but if you don’t need them, don’t pay for them. Sometimes it’s an exercise in mental gymnastics to get a section lined up with elements back-to-back, but it’s worth it.
2. Powder and air driven pins have to be shot perpendicular to the connected surface. Make sure there is enough room to get the tool in and aligned to drive the pin safely. While screws are a bit more forgiving, the same should be considered.
3. Avoid welds. Thin material is hard to weld and it’s basically bringing in a whole new trade to the jobsite.
Finally, know and understand the landlord’s structural requirements. Most malls, for instance, won’t allow bulkheads to be hung from the structure above, but do allow for attachment to framing for lateral stability. Many, however, do not allow attachment of any kind to metal roof deck.
It’s never too early to involve your structural engineer, or at least determine what the engineer’s role might be. Some things are obvious, like, “Can we place a new 1500 pound HVAC unit on the roof?” That ought to take a licensed engineer to figure out. Other things the permitting authority requires may not be so apparent. Be most aware of high seismic jurisdictions on the west coast and high wind on the east, and ask if any of the systems you plan to install require design by an engineer. Repeat offenders are bulkheads, signage, suspended ceiling systems, and, more and more frequently, shelving systems. Knowing up front and meeting local requirements early is much more pleasant for the owner than hiring additional consultants because of a plan review comment.
Plan ahead and don’t get burned!!!
Are you passionate about the AEC industry? Do you want to use your talents with a group of the greatest engineers, landscape architects, technicians and support personnel in the industry? You've found the right place. Wallace is unique in the way we strive to make lives better for our clients, communities and employees. And we believe we have more fun doing our job than just about anyone else! The art of possibility. Discover it at Wallace.
Learn More
There are no comments.